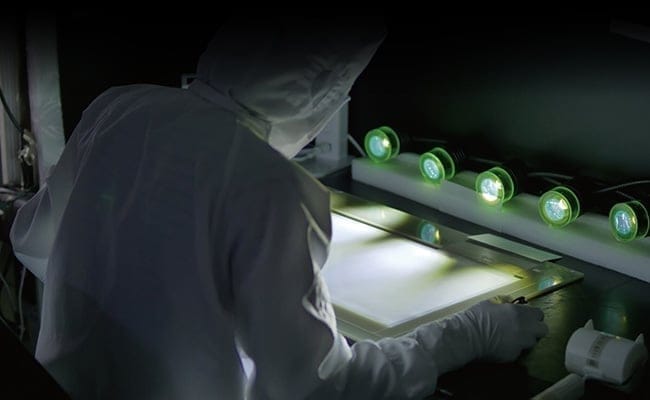
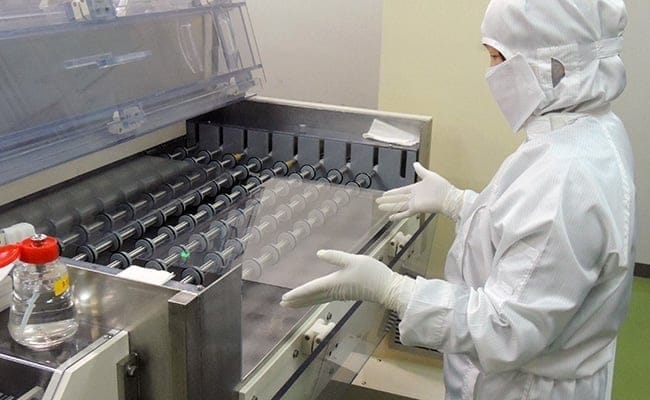
High-precision, high-quality bonding is carried out in a clean room, where everything from bonding processing to inspection is carried out in an integrated manner. Specialist facilities and equipment required for bonding, such as pressure de-aerators (autoclaves) and drying equipment, enable quality to be built up to meet the customer's requirements. We respond to the diverse needs of our customers with stable quality according to their applications.
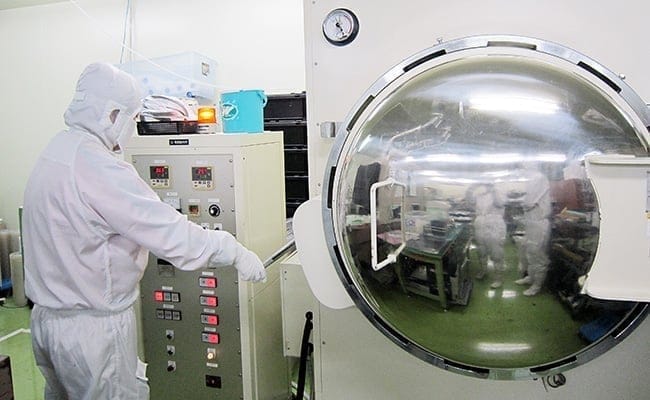
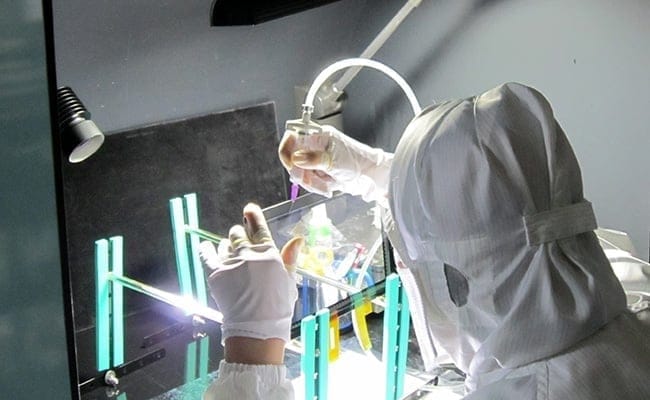
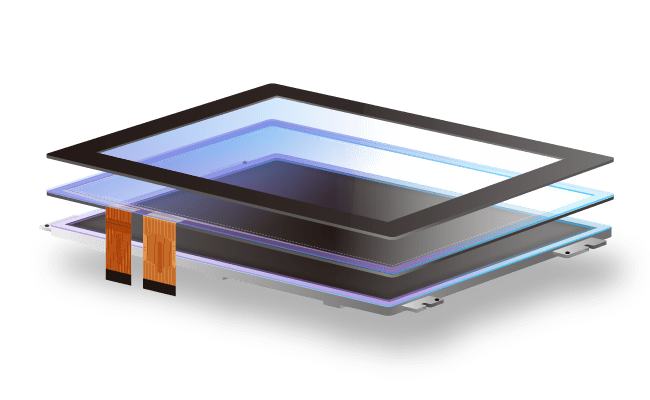
Optical bonding is a technology whereby the LCD (liquid crystal display) and touchscreen or cover glass are bonded together using a resin material (optical elasticity resin). The gap between the materials is filled with resin, eliminating even the smallest air layer and suppressing light reflection. By reducing the parallax shift caused by light reflection, the contrast is increased and visibility is improved, enabling the screen to be displayed beautifully. The resin also suppresses deformation due to stress relaxation and its high shock-absorbing properties provide excellent durability, especially for outdoor use.
-
Display screens beautifullyThe refraction of light as it passes through the air layer between the LCD, touchscreen/cover glass and the gap between them weakens the light and reduces the brightness of the image. Optical bonding minimises the refractive index of light by bonding them together without gaps using resin, thereby realising a screen display with high visibility.
-
Reduce reflections and glareScreen glare is the reflection of light with different refractive indexes that occurs when external light passes through the cover glass/touchscreen and the air layers that form in the gaps. Optical bonding minimises the refractive index of light by bonding the gaps together with resin, thereby reducing screen glare.
-
High durability and shock absorptionOptical bonding can strengthen the surface by laminating with optical elasticity resin without gaps. As there are no gaps between the LCD and the cover glass/touchscreen, damage caused by penetration of foreign substances such as water and dust, and deformation caused by stress relaxation can be physically suppressed.
-
No internal condensationIn environments with extreme temperature differences, water vapour can form in the air layer between the LCD and the cover glass/touchscreen, causing condensation. Optical bonding eliminates the effects of condensation on the display and equipment, as the air layer that causes condensation is not generated.
-
Correcting displacement due to parallaxThe thickness of the cover glass/touchscreen usually causes parallax between the LCD display and the actual visible display. Optical bonding makes it easier to match the image formation of the touch position and the display position, thus enabling accurate touch input with less displacement due to parallax.
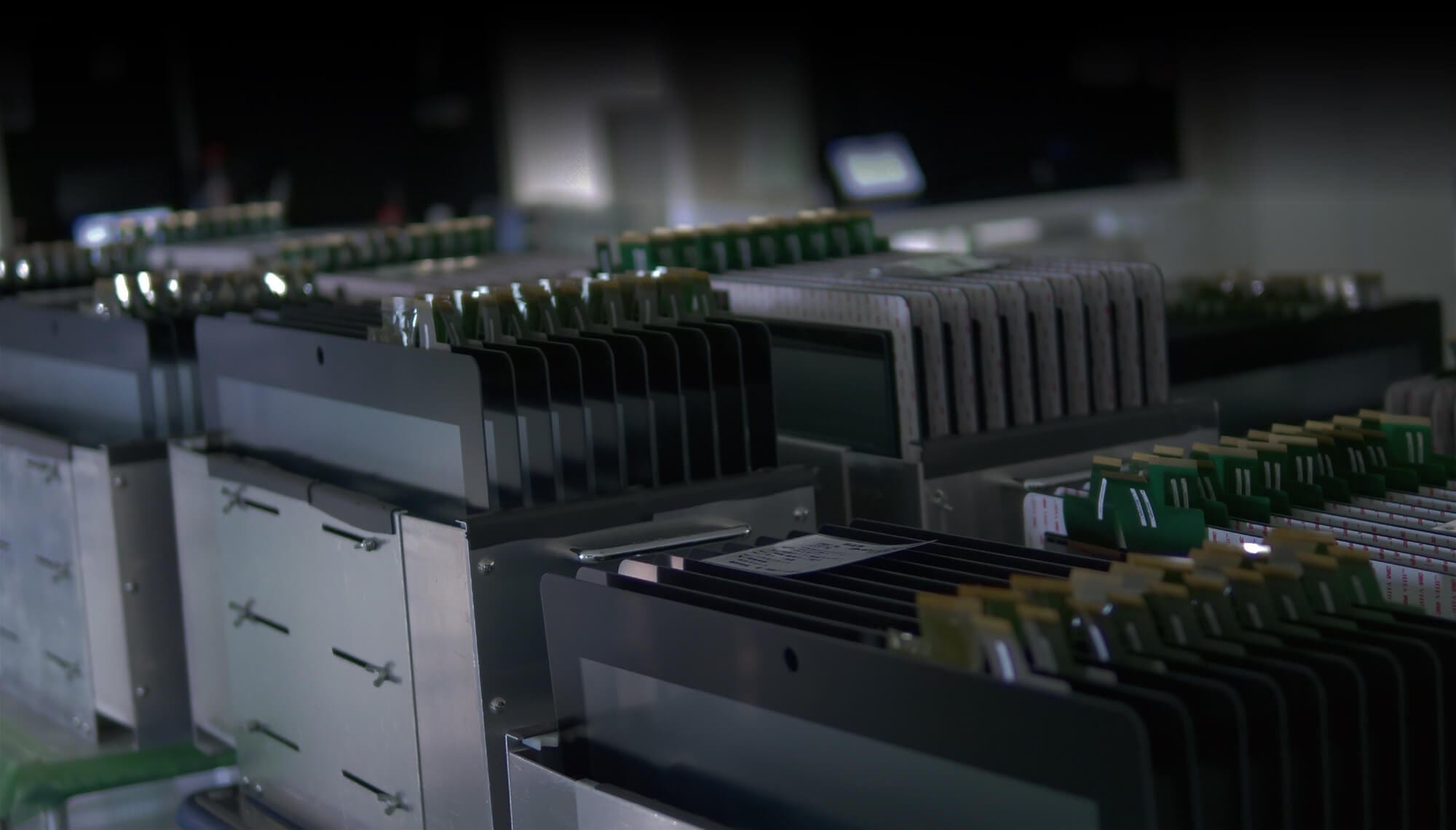
Air bonding is a standard bonding method where the touchscreen or cover glass and LCD (liquid crystal display) panel are attached to the frame area using double-sided adhesive tape. It is easy to bond, has a high yield rate and excellent cost performance. Replacement in line with the product cycle can be carried out in a relatively short period of time. This is an easy-to-use and user-friendly lamination method with sufficient durability and display visibility to withstand normal use.